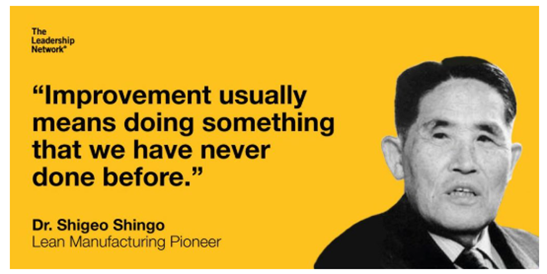
Shigeo Shingo was born in 1909 in Saga City, Japan. He studied at Yamanashi Technical College and graduated as an engineer in 1930. Shingo began his professional career at a railway company in Taipei. In 1945, he started working at the Japan Management Association (JMA) in Tokyo, where he became a consultant specializing in managing and improving production processes in factories. In 1950, he worked on improvement activities at Mazda, and in 1957, he collaborated with Mitsubishi on similar projects.
In 1955, Shigeo Shingo gave a seminar on production systems, which was attended by Taiichi Ohno, a Toyota executive and the architect of the Toyota Production System (TPS). Impressed by Shingo’s insights, Ohno invited him to work with Toyota. Shingo played a crucial role in developing Kaizen and shaping the Toyota Production System. Over 20 years, he conducted approximately 80 lectures and trained thousands of Toyota engineers.
During the 1960s, Shingo focused on preventing human errors in industrial processes related to quality issues. He was the first to implement the Poka-Yoke technique to ensure that workers would not forget to assemble parts correctly and to prevent recurring mistakes in production processes.
Shingo also worked on improving the efficiency of press machines used in manufacturing. He observed that die changes during model transitions caused significant production losses—at times, the time taken to switch dies was longer than the actual production process. To address this issue, he developed the Single Minute Exchange of Die (SMED) technique. By implementing SMED, he successfully reduced die changeover times at Toyota factories in 1969, bringing them down from 1-2 hours to just one minute.
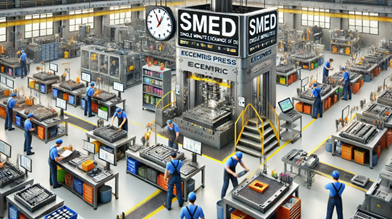
“Lean is a way of thinking, not a list of things to do”
Dr.Shigeo Shingo
Shingo’s work in the West began after he met Norman Bodek, a teacher, consultant, author, and publisher. Bodek translated and published over 100 Japanese management books into English, including the works of Taiichi Ohno and Dr. Shigeo Shingo. With Shingo’s support, Bodek developed one of the first Lean manufacturing consulting practices in the West.
In an interview, Norman Bodek shared his thoughts on Shigeo Shingo:
“Shingo was extremely determined to encourage people toward continuous improvement. The words ‘impossible’ and ‘it can’t be done’ did not exist in his vocabulary. He worked into his eighties and never retired.”
“Dr. Shingo would assign homework to his clients when he left them. Just like in school, we must learn and then apply our knowledge in the journey toward operational excellence. When he returned a month later, he expected the assigned tasks to be completed. He did not tolerate wasted time and never allowed his own time to be wasted.”
Throughout his career, Shingo traveled extensively across Europe and North America, conducting numerous conferences, factory visits, and consulting engagements. He played a crucial role in helping many U.S. and European companies implement the Toyota Production System (TPS).
Shingo authored 14 influential books on manufacturing and hundreds of articles.
In 1988, in recognition of his lifetime achievements, the Jon M. Huntsman School of Business at Utah State University established the Shingo Prize for Operational Excellence.
The 10 Fundamental Principles of the Shingo Model
Cultural Foundations
- Recognize the dignity and value of people. Valuing employees, involving them in processes, and investing in their development are essential.
- Leaders should be open to learning, listen to employees, and lead continuous improvement.
Continuous Improvement
- Think in terms of processes. Organizations should be seen as systems, and the interconnections between processes must be understood.
- Ensure continuous flow and deliver value to the customer. Business processes should be continuously improved to provide an uninterrupted value stream to the customer.
- Prevent errors at the source. Errors should be eliminated before they occur, ensuring quality assurance.
- Embrace a culture of continuous improvement. Development should be driven by cycles of hypothesis creation, testing, and learning.
- Utilize smart automation and visual management. Lean manufacturing techniques should be implemented to ensure value reaches the customer at the right time and in the right amount.
Enhanced Business Outcomes
- Align goals and strategies. Strategies at all levels of the organization should be aligned with processes.
- All systems and processes within the organization should be integrated toward common objectives.
Sustainability of Results
- Focus on ideal outcomes. Every improvement should ultimately focus on creating value for the customer.
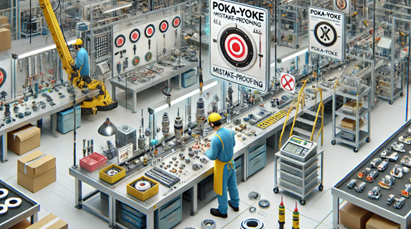
“Those who are not dissatisfied will never make any progress”
Dr.Shigeo Shingo
Final;
The methodologies developed by Shigeo Shingo have led to revolutionary changes in the manufacturing world and have laid the foundation for operational excellence across multiple industries. His teachings continue to illuminate not only past but also future production systems.
In today’s business world, adopting lean manufacturing and continuous improvement principles is an indispensable necessity for any organization seeking to achieve sustainable success and gain a competitive advantage.